Metal casting is a centuries-old process that has been utilized for centuries to create everything from weapons to coins. In modern times, metal casting facilities have become increasingly sophisticated and efficient thanks to advances in technology and quality control practices.
Quality control and testing play an essential role in ensuring the final products are of high quality and meet industry standards. This article examines the various ways that modern metal casting facilities use quality control and testing to ensure their products are of the highest caliber possible.
Materials Testing
Quality control and testing is an essential part of any modern metal casting facility. Materials testing is a key component of ensuring that the parts produced are consistent in quality and safe for use.
It can involve various methods such as mechanical, chemical, optical, or electrical tests to evaluate the properties of metals used in casting. These tests help identify potential issues about strength, hardness, weldability, porosity, and other material characteristics before they become a problem in production.
By taking the time to perform materials testing early on during the manufacturing process it assures companies that their products will meet customer expectations when released into the marketplace. Quality control teams may also track samples over time to ensure consistency with previous results or look for changes resulting from new equipment or processes being implemented at a facility.
With advances in technology continuing to make rapid strides forward all steps within the production process must remain up-to-date so customers receive only top-grade items every time they purchase from a metal casting business.
Visual Inspection of Pieces

Visual inspection of pieces is a critical step in the quality control and testing process for modern metal casting facilities. Technicians use visual inspection to identify any irregularities or defects that could compromise the integrity of each piece.
They must be able to accurately evaluate surface flaws such as porosity, shrinkage, welding problems, wear marks, oxidation, and other undesirable characteristics. Visual inspections are conducted with special magnifying devices and lighting systems that allow technicians to see fine details not visible under normal light conditions.
With the help of advanced imaging technology such as X-rays and computed tomography (CT) scans, technicians can even assess internal features like wall thicknesses and surface textures within castings for more detailed analysis. By combining traditional visual inspection methods with cutting-edge technologies, metal casting facilities can ensure their products meet industry standards while providing customers with high-quality parts they can trust.
Measurement and Calibration Verification
Measurement and calibration verification is a critical component of quality control in modern metal casting facilities. Using the most advanced tools available, technicians can accurately measure and verify the dimensions of castings as well as other objects produced in the facility.
These measurements are then compared against pre-defined tolerances or standards to ensure that all products meet customer specifications. The process also allows for any discrepancies between actual readings and expected results to be identified quickly, allowing producers to take corrective action if necessary.
In addition, regular calibrations of instruments used ensure accuracy over time and help detect potential problems before they become an issue. By combining precise measurement with careful calibration verification, metal casting facilities can guarantee high levels of quality control throughout their operations while ensuring customer satisfaction at every stage of production.
Leakage/Pressure Testing
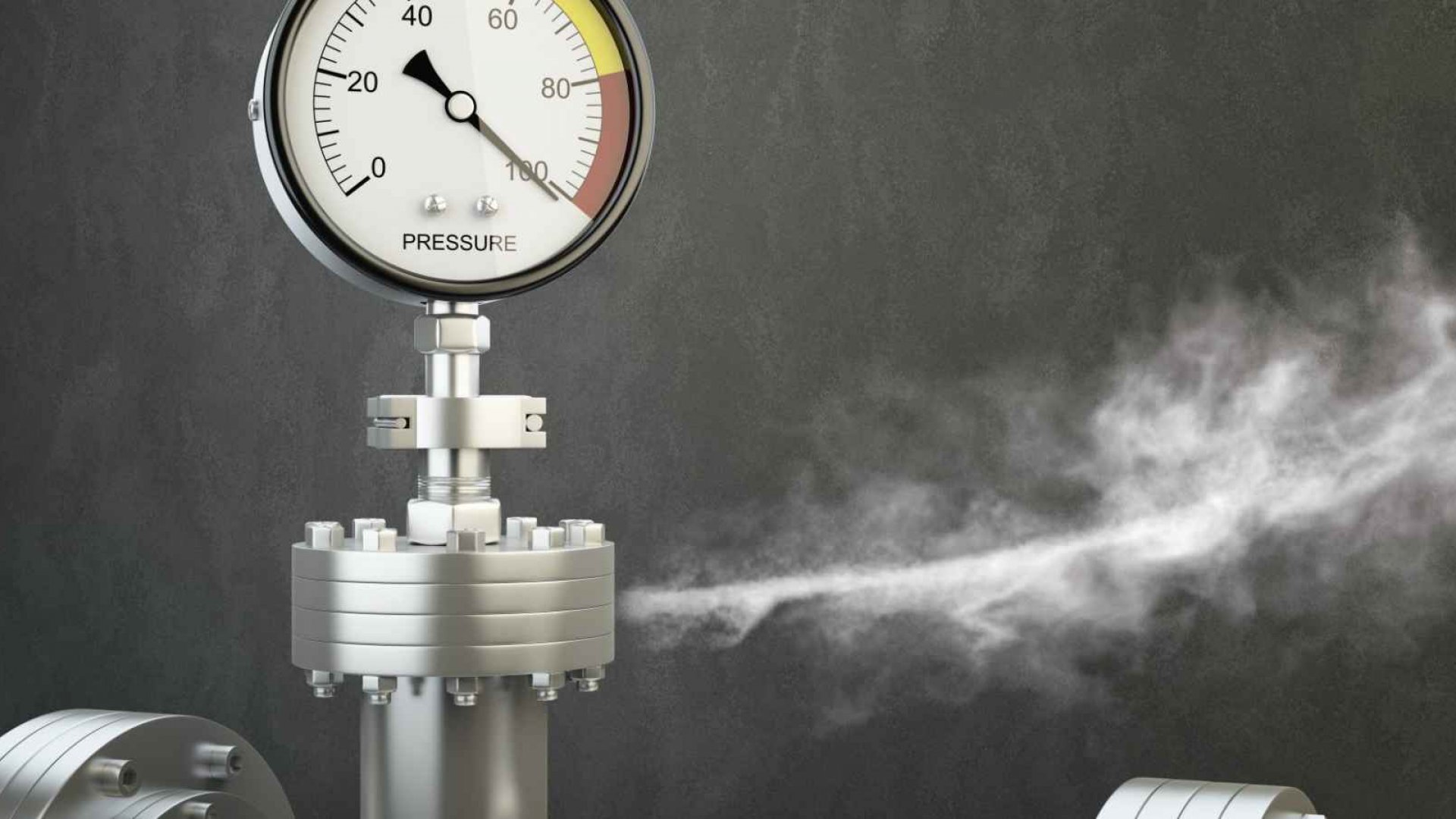
Leakage/Pressure testing is an important component of quality control and testing in modern metal casting facilities. These tests are used to detect any cracks, air pockets, or other defects that could cause a leak in the final product.
By performing these tests on raw materials before they are cast into molds, manufacturers can ensure that their products meet the highest standards for safety and reliability. Pressure testing involves applying pressure to the material being tested using specialized equipment such as hydrostatic testers and ultrasonic devices which measure any changes in resistance levels due to a defect or imperfection.
Leakage tests involve submerging parts in water tanks or enclosures filled with pressurized air or liquid so that any leaks can be detected quickly by visual inspection. Both leakage and pressure tests should be conducted regularly throughout the production process to ensure consistent quality control standards are met at all times.
Thermal Performance Evaluation
Modern metal casting facilities require accurate and reliable thermal performance evaluations to ensure the quality of their products. This evaluation requires precise measurements of material temperature, heat flux, and other parameters across a range of environmental conditions.
Testing methods such as infrared thermography can be used to identify areas where temperatures are outside an acceptable range, allowing engineers to make necessary adjustments before production begins. Thermal imaging cameras can also detect convective heat transfer or air flow that may affect product performance in different environments.
A thorough thermal performance evaluation is critical for ensuring the proper operation of metal castings in all kinds of applications.
Conclusion
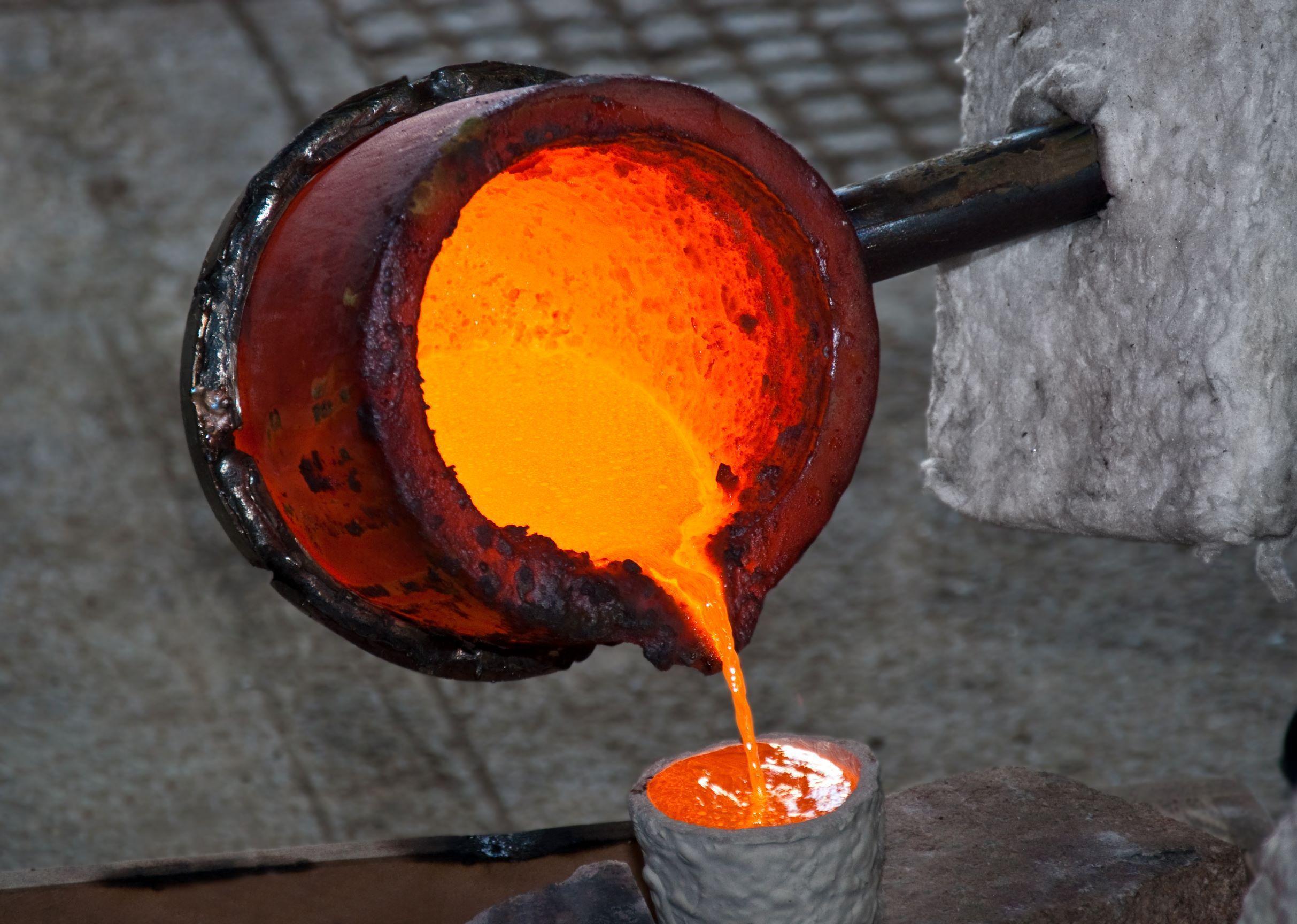
Metal Casting is an important process in modern metal casting facilities, and quality control and testing play a vital role in ensuring that the highest standards of product safety and performance are met. Quality control involves inspecting processes and products throughout production to ensure they meet required specifications.
Testing evaluates how well materials will perform under various conditions so that potential weaknesses can be identified before production begins. By using these techniques, metal casting facilities can produce high-quality parts with minimal risk of defects or other problems during use.
With careful management of quality control and testing procedures, modern metal casting facilities have what it takes to create reliable components for any application.